Precision Engineering in Action: Leading the Way as a Blow Molding Machine Manufacturer
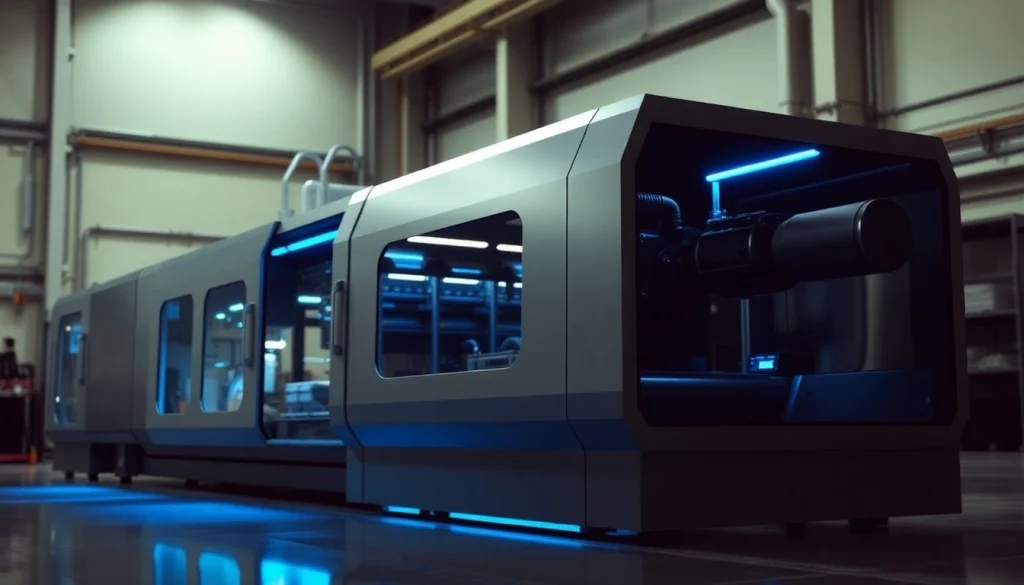
Understanding Blow Molding Technology
What is Blow Molding?
Blow molding is a manufacturing process that creates hollow plastic parts, primarily utilized for producing containers such as bottles, jars, and tanks. This innovative technique employs air pressure to inflate heated thermoplastic materials within a mold, shaping them into desired forms. The blow molding process is highly favored for its efficiency and versatility, enabling mass production of uniform items with consistent quality.
Types of Blow Molding Processes
Blow molding can be broadly categorized into three primary types: extrusion blow molding (EBM), injection blow molding (IBM), and stretch blow molding (SBM). Each process offers unique advantages depending on the application and the type of product being manufactured.
- Extrusion Blow Molding (EBM): In EBM, a tube of plastic (parison) is extruded and then inflated within a mold. This process is typically employed for producing larger, hollow containers such as drums and larger bottles.
- Injection Blow Molding (IBM): This method combines elements of injection molding and blow molding. Here, plastic is first injected into a preform shape, which is then transferred to a mold and inflated to form the final product. IBM is often used for producing small, precision containers.
- Stretch Blow Molding (SBM): SBM utilizes both stretching and blowing to create high-strength containers, commonly used for beverage bottles. The preform is subjected to axial stretching before inflation, enhancing clarity and mechanical properties.
Applications of Blow Molding Machines
Blow molding machines are extensively used across various industries due to their ability to produce a wide range of products efficiently. Key applications include:
- Food and Beverage Packaging: Bottles for water, soft drinks, and other beverages.
- Consumer Goods: Containers for household products, cosmetics, and personal care items.
- Pharmaceuticals: Bottles and containers for medications.
- Industrial Uses: Tanks for chemicals, fuel, and other industrial applications.
Choosing the Right Blow Molding Machine Manufacturer
Key Factors to Consider
Selecting a blow molding machine manufacturer is crucial for ensuring the success of your production line. Here are essential factors to consider:
- Manufacturing Experience: Look for manufacturers with extensive experience in blow molding technology and a proven track record of delivering high-quality machines.
- Machine Customization: Choose a manufacturer that offers customizable options to fit specific production needs, including size, output capacity, and automation level.
- Support and Maintenance: Assess the level of after-sales support, including installation, maintenance, and availability of spare parts.
- Technological Innovation: Evaluate the manufacturer’s commitment to innovation, as advancements in blow molding technology can significantly improve efficiency and reduce production costs.
Top Brands in the Industry
The blow molding industry features several reputable manufacturers known for their quality and innovation. Some leading brands include:
- Uniloy: A global leader in blow molding technologies, offering various innovative solutions.
- Wilmington Machinery: Recognized for high-speed rotary extrusion blow molding machines.
- Jomar Corporation: Celebrated for its expertise in injection blow molding machines.
- Bekum Maschinenfabrik: Offers a diverse range of blow molding machines with advanced technology.
Evaluating Manufacturer Reputation
Manufacturer reputation plays a vital role in your decision-making process. Research potential manufacturers by:
- Reading customer reviews and testimonials.
- Consulting industry forums and trade publications.
- Attending trade shows and exhibitions to see machinery in action and connect with peers.
Innovations in Blow Molding Machinery
Latest Technology Trends
Technological advancements are transforming the blow molding industry. Some noteworthy trends include:
- Smart Manufacturing: Integrating Industry 4.0 technologies, such as IoT and AI, enhances machine monitoring and predictive maintenance capabilities.
- Energy Efficiency: Newer machines focus on reducing energy consumption, leading to cost savings and lower environmental impact.
- Robotics and Automation: Incorporating robotics into blow molding processes increases production efficiency and maintains consistency in manufacturing.
Sustainability in Blow Production
Sustainability is becoming increasingly important in manufacturing. Effective recycling processes and the use of biodegradable materials are gaining traction:
- Recycling technologies enable the reuse of plastic materials, reducing waste.
- Manufacturers are focusing on developing machines that accommodate eco-friendly materials without compromising product quality.
Efficiency and Productivity Enhancements
Continuous improvements in machine design lead to enhanced efficiency and productivity:
- Rapid cycle times reduce production delays and enhance output.
- Modular designs allow manufacturers to scale production up or down quickly based on market demand.
Performance Metrics for Blow Molding Machines
Production Output and Speed
Choosing the right blow molding machine involves understanding its output capacity and speed:
- Output Rates: Assess the machine’s production rates per hour and how they align with your business goals.
- Speed Variability: Some machines can adjust speeds based on product size and complexity, which can optimize performance.
Quality Control Measures
Quality control is vital in blow molding to ensure consistency and meet production standards:
- Implementing inline quality testing allows for real-time adjustments during the production process.
- Utilizing statistical process control (SPC) can help monitor production and maintain required specifications.
Cost-Effectiveness and ROI
Investment in blow molding machinery involves analyzing long-term costs:
- Consider initial investment versus maintenance and operational costs.
- Evaluate the potential return on investment (ROI) based on increased production efficiency and reduced waste.
The Future of Blow Molding Manufacturing
Impact of Industry 4.0
As Industry 4.0 reshapes manufacturing landscapes, blow molding is no exception. The integration of smart technologies promises:
- Enhanced production analytics for informed decision-making.
- Better inventory management through real-time tracking of materials and outputs.
- Greater customization options in production.
Emerging Markets and Opportunities
The global demand for blow molding products is expanding, particularly in developing regions:
- Growing consumer markets in Asia and Africa are driving demand for plastic products.
- Investments in infrastructure and packaging innovation create opportunities for blow molding manufacturers.
Long-term Trends to Watch
Stay abreast of market trends that may influence the blow molding industry:
- Increased focus on sustainable practices and environmental compliance will shape production processes.
- Adoption of advanced materials, such as bioplastics, could redefine the types of products that can be manufactured.
- Automation and robotics will continue to enhance efficiency and reduce labor costs.
As a Blow Molding Machine Manufacturer, understanding these dynamics is essential for staying competitive in an evolving market. Companies that adapt to these changes and invest in advanced technologies are likely to lead the industry into the future.