Mastering Precision Die Cutting: Techniques for High-Quality Production
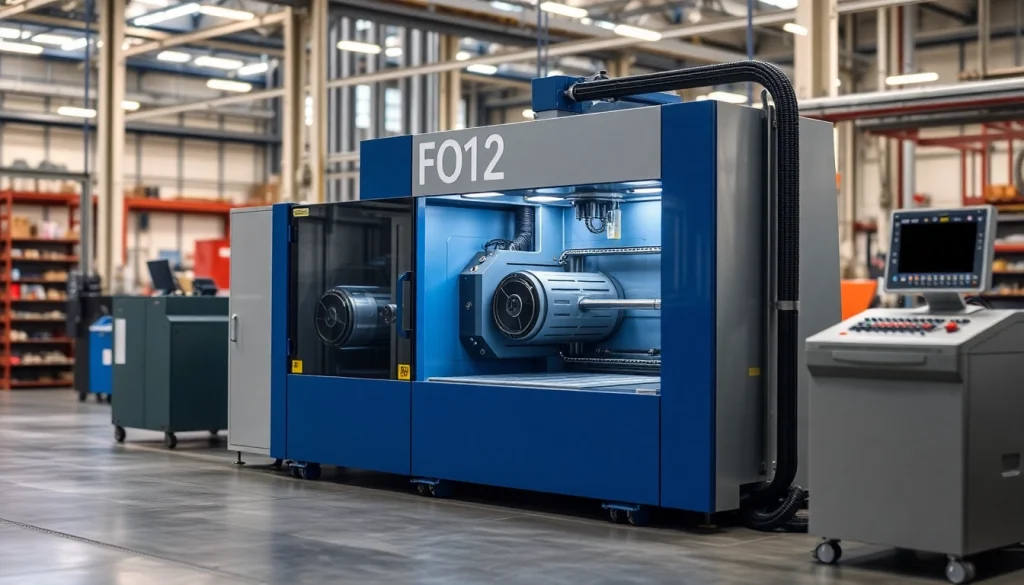
Understanding Precision Die Cutting
Precision die cutting is a pivotal technique in the manufacturing sector, enabling the creation of intricate and high-accuracy designs across multiple industries. This methodology utilizes specialized tools and machinery to precisely cut materials into specific shapes and sizes, ensuring uniformity and consistency. By integrating processes like precision die cutting, businesses streamline production, reduce material waste, and enhance overall product quality. In this guide, we will explore the nuances of precision die cutting, its applications, benefits, and much more.
What is Precision Die Cutting?
At its core, precision die cutting involves using dies—tools specifically designed to cut materials into desired shapes. This process is often characterized by its remarkable accuracy, allowing for cuts that can be as precise as a few microns. Precision die cutting can be accomplished through various methods, including rotary die cutting and flatbed die cutting, each catering to different materials and production needs.
Applications of Precision Die Cutting in Various Industries
The versatility of precision die cutting is evident in its widespread usage across diverse sectors. Here are a few notable applications:
- Automotive Industry: Used for gaskets, seals, and soundproofing materials that require high precision due to tight tolerances.
- Medical Devices: Essential for producing components like adhesive bandages, surgical implants, and specialized packaging.
- Electronics: Vital in developing insulators, cushioning materials, and EMI shields for devices.
- Consumer Products: Found in packaging, labels, and decorative elements in food and beverage industries.
Benefits of Using Precision Die Cutting Techniques
The advantages of precision die cutting are manifold, making it an attractive option for manufacturers:
- High Precision: Achieves consistent and accurate cuts, ensuring product reliability.
- Material Efficiency: Minimizes waste through optimized layouts and precision cuts that leave little excess.
- Speed: Streamlines production processes, significantly reducing lead times and improving turnaround.
- Cost-effectiveness: While there is an initial investment in die creation, the long-term savings in labor and materials often outweigh the costs.
Common Materials Used in Precision Die Cutting
Types of Materials Suitable for Die Cutting
Precision die cutting is compatible with a wide range of materials, making it suitable for various applications. Common materials include:
- Papers and Cardboards: Perfect for packaging and promotional materials.
- Foams: Used for cushioning, insulation, and soundproofing applications.
- Adhesive Tapes: Essential for creating gaskets and seals in various industries.
- Plastics: Used extensively in consumer products and electronic devices.
- Metals: Thin metals can be die cut for specific applications like electrical components.
Material Performance and Quality Considerations
When selecting materials for precision die cutting, performance and quality are paramount. Factors such as thickness, density, and flexibility can affect how well a material is cut. For instance:
- Thicker materials: Require stronger, more durable dies and potentially more advanced machinery.
- Flexible materials: May demand different cutting techniques to avoid distortion during the process.
- Material consistency: It’s crucial for maintaining quality; variations in material can lead to inconsistent cuts.
Innovative Uses of Materials in Precision Die Cutting
Innovation in materials and processes has expanded the horizons of what can be achieved with precision die cutting. Notable examples include:
- Smart Materials: These can change properties in response to environmental conditions, and die cutting can create complex shapes for integration into products.
- Composite Materials: Combining materials to leverage their strengths can also be accomplished via precision die cutting for advanced applications in aerospace and automotive industries.
Techniques and Equipment for Precision Die Cutting
Overview of Rotary and Flatbed Die Cutting Methods
Two prevalent methods in precision die cutting are rotary and flatbed die cutting, each with unique attributes:
- Rotary Die Cutting: This method uses cylindrical dies and is known for its speed and efficiency, making it ideal for high-volume orders.
- Flatbed Die Cutting: Involves a flat die that applies pressure directly to the material, offering greater flexibility for custom designs and intricate details.
Choosing the Right Die Cutting Equipment
Selecting the appropriate die cutting equipment is critical for achieving the desired precision and efficiency. Key considerations include:
- Production Volume: Higher volumes may require rotary die cutting for efficiency, while smaller runs may benefit from flatbed systems.
- Material Types: Different machines are better suited for specific materials; hence, understanding the application is vital.
- Size of the Parts: Ensure the equipment can accommodate the dimensions of the components needed.
Best Practices for Implementing Precision Die Cutting
Successful implementation of precision die cutting necessitates adherence to best practices, including:
- Thorough Design Review: Ensure designs are optimized for die cutting processes to avoid complications later.
- Material Testing: Perform trials with the selected materials to ascertain compatibility and performance.
- Regular Maintenance: Maintain equipment to ensure the longevity and performance of the cutting tools.
Challenges in Precision Die Cutting
Identifying Common Problems and Solutions
While precision die cutting is highly advantageous, it is not without challenges. Common issues include:
- Die Wear: Over time, dies can dull and lead to inaccuracies; regular inspection and timely replacements are necessary.
- Material Variability: Sourcing consistent materials is crucial; establish reliable relationships with suppliers to ensure quality.
- Complex Designs: Intricate shapes may require special dies; prepare for potential increased costs and longer lead times.
Maintaining Tolerances and Quality in Die Cutting
To ensure precision, close attention must be paid to tolerances. Recommended practices include:
- Utilizing High-Quality Dies: Invest in quality tooling to achieve better precision in production.
- Regular Calibration: Conduct routine checks to confirm that machines maintain necessary tolerances throughout production runs.
- Implement Quality Control Measures: Establish robust QA protocols that involve checking samples regularly to catch discrepancies early.
Cost Considerations and Budgeting for Die Cutting
Understanding the financial implications of die cutting is essential for effective budgeting. Key considerations include:
- Initial Die Costs: These can be significant, particularly for custom designs, but are amortized over large production runs.
- Material Costs: Pricing can fluctuate based on market demand; negotiating with suppliers can lead to better rates.
- Operational Costs: Be mindful of machine maintenance and labor costs associated with running precision die cutting operations.
Future Trends in Precision Die Cutting Technology
Emerging Technologies in Die Cutting
The future of precision die cutting looks promising with several emerging technologies on the horizon:
- Automation: Increased use of automated machinery can enhance speed and reduce labor costs substantially.
- Digital Die Cutting: Allows designers to develop prototypes quickly, creating new opportunities for customization.
- AI Integration: Artificial intelligence can help optimize cutting patterns for material efficiency, further reducing waste.
Sustainability in Precision Die Cutting Practices
As industries move towards sustainable practices, precision die cutting is no exception. Innovations in eco-friendly materials and waste reduction strategies play a crucial role. For instance:
- Recyclable Materials: Utilizing materials that can be reused minimizes environmental impact.
- Waste Reduction Strategies: Efficient layout designs can significantly decrease offcuts, contributing to sustainability efforts.
Adapting to Market Demands with New Techniques
The ever-evolving market necessitates adaptation and flexibility in techniques. Companies must be prepared to pivot towards:
- Custom Solutions: Developing specialized cuts tailored to unique customer needs.
- Faster Turnaround Times: Customers demand quicker delivery, making speed a critical factor in competitiveness.